超高強鋼熱衝壓件既可以保證安全性,又可以實現輕量化,因此在汽車中的應用越來越多。而這些汽車零件具有複雜的空間曲麵,在熱衝壓時形變劇烈,熱、力、相變等影響因素多,成形過程複雜,造成板料的應力、應變、組織分布不均勻,出現板料的過分減薄,影響零件的結構強度,甚至會出現開裂缺陷。目前,已有學者對工藝參數對板料減薄率的影響進行了研究,研究表明板料溫度、壓邊力、摩擦係數都可以影響板料的減薄率。
為了降低減薄率,保證零件的結構強度,本文提出先對板料進行預成形,從而改變熱衝壓的應力、應變分布,再完成熱衝壓。預成形件的形狀、尺寸對超高強鋼板的熱衝壓產生較大的影響,尤其是對板料的減薄率產生影響,進而影響零件的結構強度。
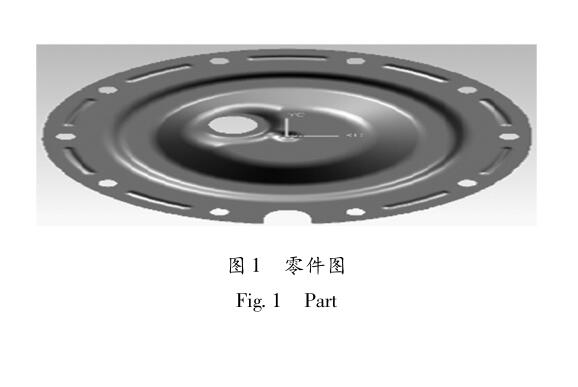
所以,有必要對超高強鋼板熱衝壓預成形進行研究。尚欣提出將超高強度鋼在不同的熱預成形行程下進行雙熱成形,得到成形後成形件厚度的分布規律,結果表明,熱預成形行程為 0. 5H (H 為行程) 時,成形件厚度分布最佳。劉文提出對高強鋼冷態下預成形,再進行熱衝壓成形出最終零件,研究成形行程對熱衝壓的影響,結果表明,預成形的行程越大,板料在第 2 步熱衝壓時,熱量散失越小,材料的塑性越好,等效應變越小,板料厚度變化越小。呂萌萌提出對超高強鋼板直接冷衝壓出成形件,再加熱進行熱衝壓,結果表明,間接熱衝壓件精度比直接冷衝壓件的精度高。
綜合以上研究現狀可知,目前對複雜汽車熱衝壓件減薄率的研究主要集中在工藝參數對減薄率的影響。對複雜汽車熱衝壓件預成形的研究,關注於預成形的行程以及熱衝壓時的工藝參數對成形性的影響,對預成形件的形狀、尺寸對減薄率的影響研究較少。
以車輪側蓋零件為研究對象,如圖 1所示,車輪側蓋為結構件,需要承受靜壓力和衝擊載荷作用,對其力學性能要求較高,以超高強鋼為其材料能夠很好滿足其力學性能要求。然而該零件形狀複雜,特別是零件中部有凹球,需要在拉深時反向成形,容易造成零件過分減薄,從而影響製件的綜合使用性能。針對車輪側蓋的結構特點,首先采用有限元方法模擬不同預成形件形狀的冷成形、熱衝壓過程,分析預成形對減薄率的影響,依據模擬結果,對車輪側蓋進行了實際熱衝壓實驗,獲得較滿意的實驗結果。